Leichtbau mit Polyurethan-Zahnriemen
Leichtbau mit Polyurethan-Zahnriemen
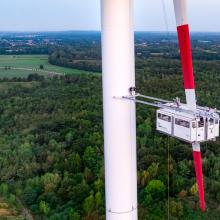
Sichere Fahrt bei jedem Wetter und zu jeder Tageszeit: das Wartungsystem terra 1.1 von WP Systems. Foto: WPS
In der Windenergiebranche bahnt sich ein kaum zu bewältigender Bedarf an Rotorblattreparaturen an. Die Lösung: ein mobiles Befahrsystem der brandenburgischen WP Systems GmbH verdoppelt die mögliche Anzahl der Wartungseinsätze pro Jahr im Vergleich zu bisherigen Systemen. Mit an Bord sind BRECO®-Zahnriementriebe, die eine bedeutende Rolle bei der Gewichtsreduzierung spielen.
Es ist ein erfreulicher Trend: mit einer Einspeisung von 100 TerraWatt aus Onshore-Windenergieanlagen lag 2018 die Erzeugung umweltfreundlichen Stroms aus der Windkraft auf Platz zwei noch vor der Atomenergie und der Steinkohle. Die rechnerische Lebensdauer von 20 Jahren übersteht die Technik aber nicht ohne Servicemaßnahmen und Reparaturen. Kaum zu fassen – aber vor allem die aus glasfaserverstärktem Kunststoff bestehenden Rotorblätter leiden unter Erosion, Blitzeinschlägen und Rissbildungen aufgrund der hohen Wechsellasten.
In Deutschland werden in der Regel alle zwei Jahre die Rotorblätter von Servicetechnikern mit der Seiltechnik inspiziert. „Eine Reparatur am Seil hat sich jedoch nicht bewährt und eine fachgerechte Laminatreparatur aus dem Seil heraus ist eigentlich nicht machbar“, weiß Ole Renner, einer der beiden Geschäftsführer von WP Systems, einem Unternehmen, das sich auf die Instandhaltung von Rotorblättern und den Rückbau von Windenergieanlagen spezialisiert hat. Er ergänzt: „Der Trend geht hin zu mobilen Befahranlagen. Stand der Technik sind heute offene Befahranlagen, d.h. offene Gestelle, die stark an mobile Arbeitsbühnen erinnern. Sie werden mit einem Rahmen am Turm abgestützt mit Winden am Rotor hochgezogen. Mit diesen einfachen Befahranlagen können die Servicetechniker die Rotorblätter schleifen, mit Polyesterharz laminieren und mit dem Coating versiegeln."
Das Problem: für die Verarbeitung der Laminate und der Harze darf es so gut wie nicht regnen und die Temperatur nicht unter 12 °C liegen. Im Winter sind so Rotor-Reparaturen praktisch nicht möglich und während der Übergangszeiten nur wenige Stunden pro Tag nutzbar. Bei Windgeschwindigkeiten über 12 m/s kann ebenso keine Reparatur durchgeführt werden.
Ole Renner erklärt dazu: „Diese drei Faktoren schränken die bislang möglichen Servicetage durchschnittlich je nach Standort auf nur 60 bis maximal 100 Tage ein. Das hat unsere statistische Analyse der Wetterdaten für mehrere Windparks ergeben. Für die Branche ist dieses Saisongeschäft mit allein 30.000 Anlagen in Deutschland eine sehr große Herausforderung.“
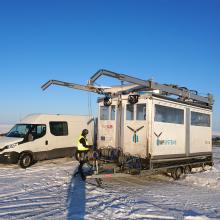
Der Tandem-Achs-Trailer mit der Befahranlage System terra 1.1 von WP Systems in Schweden. Die 3,5 Tonnen zulässiges Gesamtgewicht dürfen nicht überschritten werden. Foto: WPS
Konzept für das System terra 1.1
Holger Müller, langjähriger Experte auf dem Gebiet der Windenergie und Geschäftsführer von WP Systems erklärt die Idee der Befahranlage System terra 1.1 so: „Unser Ansatz war es, ein komplettes System zu entwickeln, mit dem ein ganzjähriges Geschäft am Rotorblatt möglich wird. Das setzt nicht nur eine, sondern gleich mehrere Innovationen voraus:
- Für eine trockene Umgebung der Reparaturstelle muss die Befahranlage das Rotorblatt wasserdicht umschließen können. Darüber hinaus muss sich der Mechanismus an unterschiedliche Konturen und Querschnitten anpassen lassen.
- Eine Lösung für die Verarbeitung des Harzes bei niedrigen Temperaturen muss gefunden werden.
- Die Befahranlage soll mit üblichen Tandem-Achs-Trailern transportierbar sein. Damit ist das Gewicht von Trailer und Befahranlage auf 3,5 Tonnen beschränkt.
Mit diesem anspruchsvollen Ziel vor Augen gründete ein interdisziplinäres Team aus Maschinenbauern, Werkstoff- und Leichtbau-Experten sowie Spezialisten für Simulationen 2015 die WP System. Innerhalb weniger Jahre setzte das junge Team mit System terra 1.1 sämtliche Anforderungen um und erfüllte auch die hohen Anforderungen für eine Zertifizierung, die auch Nachteinsätze einschließt.
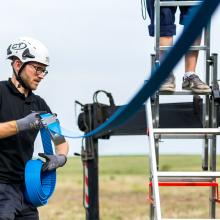
Der 15,5 Meter lange Abdruckrahmen besteht aus mehreren Segmenten, um den Transport auf dem Trailer zu ermöglichen. Gut, dass der ebenso lange Zahnriemen einfach auf- und abgerollt werden kann. Foto: WPS
Konstruktive Lösung der Befahranlage System terra 1.1
Die neuartige Befahranlage System terra 1.1 ist eigentlich eine mobile Werkstatt. Sie besteht aus einer Aluminium-Leichtbaustruktur, die mit Planen und Türen zu einer winddichten Arbeitskammer verschlossen werden kann und mit allem Nötigen wie Strom, Licht, Werkzeug und Reparaturmaterial ausgerüstet ist.
Um die Lücke zwischen dem Rotorblatt und dem Boden bzw. der Decke flexibel überbrücken zu können, entwickelte man in Ruhland verschiebbare Blenden, die der aerodynamischen Kontur der Rotorblätter angepasst sind. Sie lassen sich bis auf wenige Zentimeter nah an jedes Rotorblatt positionieren.
Eine Gummiplane mit Saugnäpfen dichtet den verbleibenden Spalt zwischen Blenden und Rotorblatt dicht ab. Damit sind Reparaturen nun auch bei Regen gut durchführbar.
Um das Harz auch an Tagen mit Temperaturen unter 12 °C verarbeiten zu können, verwenden die Entwickler bei WP Systems zum Aufheizen der Reparaturstelle Infrarotstrahler. Innerhalb weniger Minuten sind so auch bei sehr niedrigen Außentemperaturen über 30 °C erreicht.
Polyesterharz und Härter werden außerdem in einer beheizbaren Transportbox gelagert, so dass die Temperaturkette niemals unterbrochen wird. Derart präpariert sind nun auch Reparatureinsätze dauerhaft bis 0 °C, kurzzeitig auch bis -10 °C möglich.
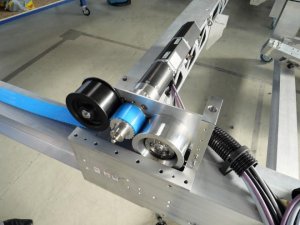
Für feuchte und nasse Umgebungen gut geeignet und besonders leicht: Aluminiumprofile und der BRECOprotect®-Zahnriemen. Dank der großen Übersetzung des Servogetriebes kann ein kleiner, leichter Motor mit integrierter Bremse eingesetzt werden. Foto: Mulco
Größte Herausforderung: Gewichtsreduzierung
Ole Renner erklärt zu den Zielkonflikten: "Obwohl wir von Anfang an die Möglichkeiten des Leichtbaus konsequent nutzten, mussten wir uns dennoch für den Antrieb des Hohlprofilrahmens auf dem 15m langen Abdruckrahmen etwas Neues einfallen lassen, um das Zielgewicht zu erreichen. Zahnstangenantriebe aus Stahl sind hier schlicht zu schwer. Ein systematischer Vergleich möglicher Antriebsarten zeigte uns schnell das Leichtbaupotenzial des Zahnriementriebes.“
André Schmidt, Vertriebsingenieur von Wilhelm Herm. Müller, zum Start des Projektes: „Der Plan von WP Systems war einfach und genial: Der Zahnriemen wird an den Enden des Abstützrahmens festgespannt und ein Omega-Zahnriementrieb auf dem Trägerrahmen verschiebt die Arbeitskammer in die gewünschte Position. Nach unserer ersten Auslegung kam jedoch „das böse Erwachen“.
Die berechnete Vorspannkraft war so hoch, dass sie die zulässigen Kräfte für den Abstützrahmen – insbesondere in der oberen Position der Befahranlage nahe an der Rotorwelle – deutlich überstieg und die Gefahr des Ausknickens bestand.
Eine stärkere Dimensionierung der Profile kam schon aus Gewichtsgründen nicht in Frage.
André Schmidt: "Wir haben daraufhin WP Systems vorgeschlagen, die beiden Riemenumlenkungen des Omega-Antriebes so eng an die Riemenscheiben zu positionieren, dass eine Zwangsführung des Zahnriemens um die Riemenscheibe entsteht. Dann kann man bei dieser Anwendung auch auf die Vorspannung verzichten.“
Ole Renner: „Diese Modifikation war für uns wichtig und sehr sehr hilfreich. Der Abstützrahmen konnte in seinen Abmaßen beibehalten und so das Zielgewicht am Ende erreicht werden."
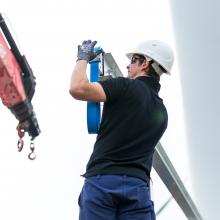
Der Zahnriemen ist mit einem Klicksystem in Windeseile montiert. Foto: WPS
Zahnriementriebe für die Abstützung und Drehung der Arbeitskammer
Für die Bewegung der Kammer entlang am Rotorblatt mussten hauptsächlich drei Bewegungen realisiert werden: die Höhenverstellung mittels Seilwinden, die Bewegung und Abstützung zum Turm mittels Abstützrahmen und die Drehung der Kammer um ihre Hochachse, um der Kontur des Rotorblattes optimal folgen zu können.
Für die Drehung der Kammer hängt diese über Laufrollen an zwei C-Bogenprofilen.
Die Bogenprofile sind wiederum mit einem Aluminium-Hohlprofilrahmen verschraubt. Dessen längsseitige Hohlprofile werden auf dem 15,5 Meter langen Abstützrahmen geführt.
Eine besondere Herausforderung bei der Entwicklung bestand darin, das zulässige Gesamtgewicht des Tandemachs-Trailers von 3,5 Tonnen nicht zu überschreiten.
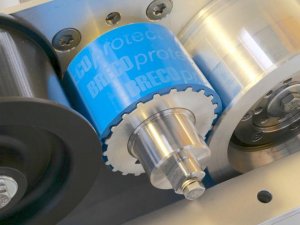
Kleiner Kunstgriff - große Wirkung: Zwangsführung des Zahnriemens um die Riemenscheibe. Foto: Mulco
Stabil und witterungsunempfindlich: BRECOprotect®
André Schmidt erklärt zur Auswahl eines geeigneten Zahnriemens: „Standard-Zahnriemen verfügen über sogenannte Wickelnasen im Zahngrund. Dort liegen die Stahlzugträger frei und bei feuchter Umgebung tritt hier Korrosion auf. BRECO bietet auch rostfreie Edelstahlzugträger an, jedoch erreichen sie nicht die Festigkeit des Stahlzugträgers. Mit der Edelstahl-Variante wäre der Antrieb daher breiter und schwerer geworden. In diesem Fall war die BRECOprotect-Meterware mit dem rundum geschützten Stahlzugträger die ideale Lösung, auch weil das verwendete Polyurethan besonders beständig in feuchter Umgebung ist.“
Für die Drehung der Gondel wählte WP Systems das gleiche Antriebsprinzip. Dort ist der Zahnriemen auf der Innenseite des gebogenen C-Profils aufgespannt und an dessen Enden befestigt, dazwischen befindet sich wieder ein Omega-Antrieb. André Schmidt zu dem weiteren Potenzial dieser Antriebslösung: „Wie man an diesem Beispiel schön erkennt, lassen sich mit einem Omega-Zahnriementrieb auf einem Kreissegment auf einfachste Weise Dreh-, Turm- und Schwenkantriebe für nahezu beliebig große Durchmesser realisieren. Der Antrieb bedarf keinerlei Schmierung und ist korrosionsfrei.“
Ole Renner über die letzten drei Jahre der Zusammenarbeit mit Mulco-Vertriebspartner Wilhelm Herm. Müller (WHM) und den bisherigen Felderfahrungen: „Wir sind sehr zufrieden mit dem Antrieb, insbesondere welch große Zugkräfte die BRECO-Zahnriemen bezogen auf ihr Gewicht übertragen können. Das ist beeindruckend. Auch unsere vielen Detailfragen während der Entwicklung wurden von Herrn Schmidt und vom Hersteller BRECO ungewöhnlich schnell beantwortet und Lösungen gefunden. Der Windenergiebranche können wir nun eine mobile Gesamtlösung für Rotorblattreparaturen anbieten, die durchschnittlich an gut 200 Tagen eingesetzt werden kann. Damit lässt sich mit dem gleichen Personalaufwand die doppelte Anzahl an Reparaturen durchführen und ganz einfach der Umsatz verdoppeln. Daran hatten die BRECO-Zahnriemen auch ihren Anteil.“
Garbsen, 15. 03.2019
Mulco-Europe EWIV