Water jet cutting for timing belts: An extremely clean and precise cut
Water jet cutting for timing belts: An extremely clean and precise cut
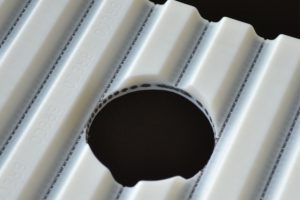
BRECO® transport belts finished with water jet cutting. Photo: BRECO
Timing belts for transport drives are usually not standardised products. Approximately 70 % of PU timing belts produced by BRECO require customisation. The great challenge posed by this fact is the need to develop a flexible, yet economically viable method for timing belt finishing. One important step toward a solution was further developing the water jet cutting method. The advantages of this method include: Greater precision, lower cost, shorter delivery times.
Technical contribution by Dr. Thomas Steinert, director of BRECO Antriebstechnik Breher GmbH & Co. KG
The increasing diversity of products in the consumer goods segment requires increased flexibility in automated production. Accordingly, an ever-growing variety of timing belt transport drives is required for these production systems. At the same time, the machine engineering industry demands shorter delivery times. However, processing timing belts, e.g. by adding holes and contours, is relatively time-consuming and costly and anything but trivial. After all, you are dealing with a composite of two entirely different materials: On the one side you have relatively soft polyurethane, on the other side there are high-tensile, relatively hard steel tension members. Depending on the task at hand, BRECO uses different finishing methods.
Drilling, milling, die-cutting
Conventional machining methods such as drilling and milling are particularly suitable for PU and are commonly used for pockets and similar tasks. However, the milling cutters must not come in contact with the tension members in the timing belt. The fine filaments would cause the milling cutter blades to wear down prematurely and, in the worst case scenario, wrap around the milling cutter, causing the tool to break. That is also why drilling is only possible in areas that contain no tension members. Unlike these machining methods, die-cutting makes it possible to break through the PU and the tension members. However, die-cutting creates high passive forces prior to the actual cutting or shearing process, causing the soft plastic to deform and be pushed aside. This becomes particularly noticeable from visible constrictions on the cut faces when working with a large wall thickness. For this reason die-cut contours are less precise than machined contours. Die-cutting is e.g. suitable for connecting two timing belt ends. The die-cutting process gives them a finger-like contour, then they are welded to each other.
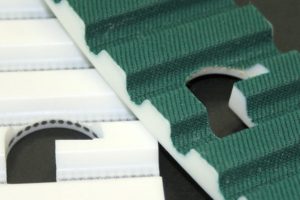
Water jet cutting achieves highly dimensionally stable contours and particularly angular cutting faces. Coating with polyamide is also possible. Photo: BRECO
Water jet cutting
Compared with the two above-mentioned methods, the great advantage of water jet cutting is its ability to cut any required contour through both materials without additional tool costs. This method does not generate the otherwise common passive forces that are inevitable in die-cutting. It also does not create burrs, which always appear on the outlet side of the milling tool during machining.
The contours are highly dimensionally stable and the cut faces are particularly angular. Thanks to quick drying after the cut and the excellent corrosion protection, corrosion is not an issue despite contact of water with the cut tension members. The fine filaments consist of high-alloyed steel and are galvanised separately. So far there have been no complaints about tension member corrosion.
From a technological perspective, water jet cutting is an excellent but unfortunately costly and high-maintenance method.
Intermittent process limits economic viability
As the travel distance of the X axes on milling, drilling and water jet cutting machines is limited, timing belts can only be processed in sections of 500 to 750 mm without further tools, depending on the table size of the machine. Once the machine has processed the hole pattern, the operator releases the clamping device, manually moves the timing belt by one processing length, re-clamps it and starts the next processing pattern. It is not unlikely for a PU timing belt of 30 m length to require 1200 holes to be cut. The particular challenge posed by processing timing belts – whether they are milled, drilled, die-cut or cut with a water jet – is the large percentage of the overall processing time constituted by the set-up time alone.
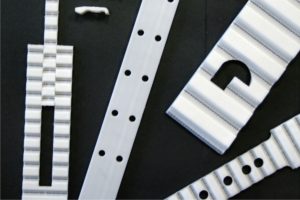
One method, many options: Water jet cutting opens up a range of new solutions. Photo: BRECO
Continuous process for greater economic viability
Many years ago BRECO began to create special timing belt drives adapted to its drilling and milling machines. They accommodate the PU timing belt being processed. The timing belt is cycled beneath the tool in the X direction based on the drilling or milling pattern or pitch. The timing belt is positioned in relation to the tool either by toothed hold-down units or directly by the timing belt drive. To process open-length BRECO products, they are turned into endless belts in a preliminary welding process, then separated again once processing is complete. As the timing belt circulates in the machine, frequent time-consuming reclamping is no longer required and the process is continuous up to the last drilling step. We use this process for milling and drilling of belt lengths between 1.1 m and 32 m, but an additional attached cascading belt deflection system permits upward expansion up to 193 m.
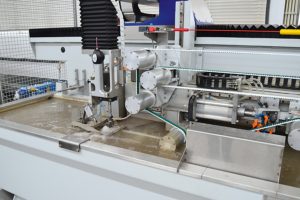
The cutting process is completed fully automatically under water. Adjustable deflection pulleys expand the range of belt lengths to an impressive 14.5 m. Photo: BRECO
Newly developed water jet cutting machines for timing belt processing
To make customised yet cost-effective processing of BRECO® timing belts possible, BRECO has transferred the integrated drive for processing belts, which has been used with great success for years in machining, to the water jet process as well. Unfortunately converting conventional water jet cutting machines proved to be impossible, so a new development in collaboration with a special machine engineering company was required. The requested conversion involving a belt drive running underneath the water jet posed the structural issue of how to prevent the lower run from being hit by the water jet. Possible solutions were a belt run guided upward around the cutting head or a wear plate between the upper and lower run to “catch” the water jet. A preliminary study showed us that small and medium belt lengths require water jet cutting particularly often. For this reason, achieving the smallest minimum belt length possible was particularly important. Guiding the belt drive over the cutting head would have resulted in minimum lengths of approx. 2.5 m. That is why we chose the wear plate solution. To minimise the time required for switching to a different timing belt profile, the timing belt is positioned using a servo drive. An adjustable belt deflection expands the maximum belt length to impressive 14.5 m. The minimum length, however, is only 1.1 m.
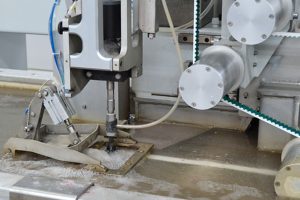
An inclined wear plate is located under the timing belt in the cutting head area to deflect the jet and prevent the lower run from being hit by the water jet. Photo: BRECO
Lower costs and greater precision
The new machine lowers the cutting cost for large numbers of holes significantly. Compared with the intermittent process on a conventional water jet cutter, the machining time for the timing belt of approx. 6 m length shown here is approximately 70 % lower on the new machine. The new machine is being used with great success. BRECO is able to employ the automated water jet cutting process for a broad range of belts and can pass on the reduction in cost to its customers. As this new method also reduces the overall production times, BRECO expects delivery times for PU timing belts requiring extensive finishing to be reduced by approximately one week.
Garbsen, 24.08.2022
Mulco-Europe EWIV