Reducing electricity costs by 80 %
Reducing electricity costs by 80 %
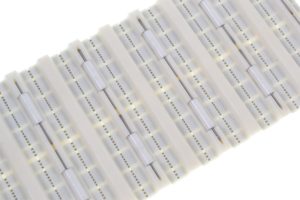
Tooth meshing behaviour of BRECOroll. Diagram: BRECO
Innovative polyurethane roller belt BRECOroll for material transport systems
Everyone is talking about energy costs but the options for saving are limited. BRECOroll, an innovation by BRECO Antriebstechnik in the town of Porta Westfalica, gives the industry a way to significantly reduce energy consumption in plants that have long transport belt drives and to build smaller, lower-cost drive motors.
Timing belts used to transport materials are usually very long. The load run of the belt is almost always supported by a support rail, which guides the belt on its sides and absorbs the weight of the workpieces on the belt and of the belt itself. This generates friction between the belt and the support rail.
The greater percentage of the drive power is used to overcome this self-inhibiting behaviour of the system. During this process, the drive is subject to major forces, generates heat and runs at a low degree of efficiency.
For this reason, timing belts for material transport come standard with a backing on the tooth side. This reduces the coefficient of friction between the timing belt and the support rail from μ=±1,0 auf μ=0.5 to 0.6. By cutting the friction in half, timing belts achieve high running performance with a low rate of wear.
However, the remaining energy consumption caused by the friction between the timing belt and the support rail is still significant. Due to the low drive power of the motors, between 0.38 and 2 kW, energy consumption has so far been largely ignored in a practical context. But this is a mistake, as our brief example calculation will show:
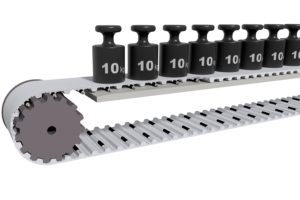
Graphic: BRECO
Example calculation of friction loss
If a conveyor belt transports 20 workpieces weighing 10 kg each, i.e. a total load of 200 kg at v=1 m/s, the power or friction loss is Pᵥ:
Pᵥ=μ ∙ m ∙ g ∙ v
=0,5 ∙ 200 kg ∙ 10 m/s² ∙ 1 m/s
=1 kW
Conventional worm gear motors have a total efficiency of approximately 0.75. The efficiency of the belt drive (without support rail) can be disregarded. This means that, for the friction loss between the belt and the support rail alone, the motor in our example has to provide 1.0 kW/0.75 = 1.33 kW. In single-shift operation, the yearly machine operating time taking into account averages for holidays, annual plant shutdowns, sick days, servicing, etc. is approximately 1.600 hours. This means the annual power consumption resulting from friction in single-shift operation amounts to a total of 2.133 kWh per belt drive. This corresponds approximately to the annual power consumption of a 2-person household. When several belt drives operate in 2/3 shifts, the losses rise to a degree that should not be disregarded in light of operating costs and the CO2 footprint. So how do you solve this problem?
From sliding to rolling friction
The idea of transferring weight forces to the support rail through rollers rather than through a sliding tooth tip is obvious, but by no means a trivial solution. Concepts involving rollers in the support rail proved to be too costly and had negative effects on the function of the timing belt. The solution: Integrating the rollers in the belt tooth.
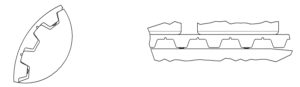
PU roller belt BRECOroll
Photo: BRECO
Tooth mesh in the pulley does not change
One basic prerequisite for the position of the rollers is that they must protrude over the tooth tip so that the rollers and not the tooth tips make contact with the support rail. To prevent the rollers from lifting the timing belt when entering the pulley and thereby generating strong constraining forces, the T20 was selected. The T timing belt is what is referred to as a “gap carrier”. The tooth tips of the belt do not touch the tooth root of the pulley. On the T20 this gap is 0.8 mm. This means the roller can protrude from the tooth tip by less than a tenth to fulfil its function of transferring the forces on the support rail. The roller practically “floats” freely in the tooth gap of the pulley. The roller diameter is dimensioned so that it does not protrude beyond the tooth flank. This allows the BRECOroll T20 to run perfectly in any standard pulley. By the way: The tension members are not interrupted by the roller.
Reducing the coefficient of friction
The BRECOroll offers a coefficient of friction of +-0.1, meaning that, compared with a PAZ-backed timing belt, it only generates 20 % of the initial loss (0.2 kW). In our example calculation, the BRECOroll would reduce the annual loss of 2.133 kWh per belt in single-shift operation by an impressive 1.706 kWh. And: It becomes possible to use a drive motor that is 0.93 kW (0.8 kW/0.75) smaller.
The BRECOroll can be used for speeds of up to 1 m/s and with area loads of up to 3 kg per roller (3kg/ 40 cm²). These limits are entirely sufficient for most material transport tasks in automated production processes. As the BRECOroll is based on a standard T20 timing belt, this is a product that has been tried-and-tested hundreds of thousands of times and will help operating companies reduce the operating cost and CO2 footprint of their plants thanks to reduced friction losses.
Garbsen, 11.05.2023
Mulco-Europe EWIV