Hyperspeed
CONTI® SYNCHROCHAIN CARBON drives the hyperloop system HyperPodX
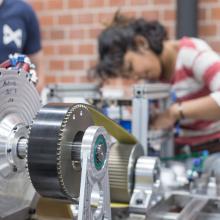
Students of the cooperative degree program Engineering Physics of the University of Applied Sciences Emden/Leer and the University of Oldenburg develop the future of mobility with their HyperPodX. Photo: CONTINENTAL
The hyperloop is a high-speed traffic system based on pods moving at close to the speed of sound on an air cushion through a tube maintaining a partial vacuum. Students of the cooperative degree program Engineering Physics of the University of Applied Sciences Emden/Leer and the University of Oldenburg have developed a hyperloop for the development project “HyperPodX”, which was organised as a competition by the American company SpaceX. Its drive contains a heavy-duty timing belt CONTI® SYNCHROCHAIN CARBON by Continental.
The hyperloop system would permit transport of people and goods at speeds of over 1,000 km/h - speeds comparable to those of aircraft.
But the hyperloop system would offer advantages over air transport: The hyperloop is significantly more environment-friendly and could run on the schedule of an underground train.
The technological concept is based on using tubes to reduce the resistance experienced by conventional trains in order to achieve far higher vehicle speeds.
In particular, the air resistance is reduced to nearly zero.
The air pressure within the tubes is at only one percent of the usual atmospheric air pressure. Moreover, no friction can be generated by wheels, as the hyperloop does not need them. Instead, the pod-shaped vehicles move by using magnetic levitation technology or air cushions.
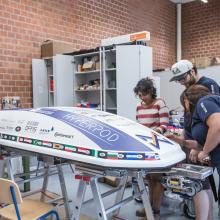
High-performance timing belt CONTI® SYNCHROCHAIN CARBON driving the HyperPodX. Photo: CONTINENTAL
Practical hyperloop projects conceivable in the near future
Covering a distance of 1,000 kilometres in just one hour? The idea of using a transport system capable of such feats between production locations worldwide opens up a vast array of new possibilities for the logistics industry.
“Another three to five years will pass before the first hyperloop will actually be usable for transporting goods,” predicts Prof. Dr. Walter Neu, hyperloop expert at the University of Applied Sciences Emden/Leer. “Various test tracks are currently under construction, for instance in France or in the United Arab Emirates. A track from Vienna to Prague is also under discussion.”
If hyperloop technology proves to be feasible in these locations and practical projects can be implemented, companies will not just profit from significantly faster transport of goods compared with current rail or road-based transport. Due to its low friction, the hyperloop requires only a fraction of the energy of conventional transport means, making it both an economical and a sustainable solution.
Moreover, it will reduce the load on roads and rails. In the long term, the hyperloop is also intended for passenger transportation.
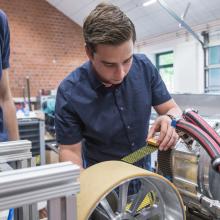
Applications engineer Alexander Behmann, Continental, provides the students with hands-on support with their timing belt drive design. Photo: CONTINENTAL
Heavy-duty timing belt CONTI® SYNCHROCHAIN CARBON fulfils hyperloop demands
The young talents at the University of Applied Sciences Emden/Leer and the University of Oldenburg under the leadership of Professors Walter Neu and Thomas Schüning researched ways of achieving these high speeds safely and reliably. Their specific task assigned by the SpaceX competition: developing a hyperloop prototype with a drive capable of both powerful acceleration and braking in a vacuum and equipped with its own energy supply. The students conquered this challenge with a 170 kW electric motor. It is capable of accelerating the 250 kg prototype to peak speeds of up to 500 km/h.
The drive required a high torque and an incredibly powerful belt. This made it the perfect task for the timing belt CONTI SYNCHROCHAIN CARBON produced by Continental, which was developed for extreme demands. Its material properties allow it to reliably cope with the high acceleration forces of the hyperloop and use in a vacuum.
“The carbon cord and polyurethane design makes this belt extremely energy-efficient, while allowing a very narrow and therefore very lightweight design. Moreover, it is highly reliable even without maintenance. These are precisely the aspects - power, reliability and low weight - that the hyperpod demands. So we were able to offer the students the perfect solution,” says Alexander Behmann, applications engineer at Continental.
The belt has already passed the first practical test: The test runs on the SpaceX tracks in Los Angeles were successful, putting the team of machine engineering and electrical engineering students of the University of Applied Sciences Emden/Leer among the top 10 ranks of the competition.
This report was included courtesy of CONTINENTAL.
Mulco-Europe EWIV
Garbsen, 21 February 2019