Of full moon nights and high-end customer service
Of full moon nights and high-end customer service
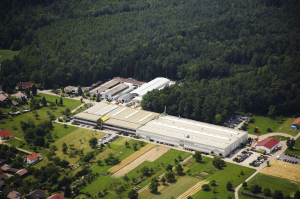
Glaston Germany GmbH in Neuhausen. Photo: Glaston
Development of polyurethane timing belts for the glass industry
The editorial team of Mulco was on the go for you once again – on the hunt for an interesting story. Situated on a hill in the beautiful northern Black Forest, we visited Glaston, one of the world's leading manufacturers of insulating glass systems. Here, we learnt a lot about the significance of dishing and full moon nights and about the extraordinary interrelationship between Glaston and the two Mulco partners, BRECO Antriebstechnik, manufacturers of polyurethane timing belts, and Hilger u. Kern as sales partner and supplier of drive elements.
Arrival in the northern Black Forest. Only a zealously crowing rooster breaks the idyllic silence in the car park. As a layman, you would never guess that state-of-the-art production machines for high-quality insulating glass are developed, produced and shipped all over the world here in Neuhausen. We are due to meet Stephan Kammerer, Head of Mechanical Design, Martin Anthoni, Head of Purchasing at Glaston, and René Preßler, long-standing technical customer consultant at Hilger u. Kern, who was able to organise the meeting thanks to his good connections.
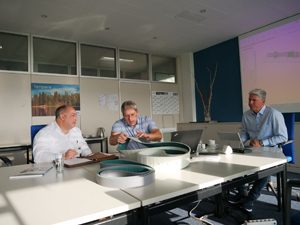
(from left to right:) René Preßler, Stephan Kammerer and Martin Anthoni are immersed in technical matters. Photo: Krismeyer
René Preßler opens our round of discussion with a look back: The start of a closer collaboration between Hilger u. Kern and Glaston goes back to a development project with the so-called heavy-duty belt, the Breco ATS15. This belt transports and positions sharp-edged glass panes, sometimes weighing several tonnes, almost vertically on its back. For this application, Breco developed a customised, stiffer tension member – important for positional accuracy – and applied a backing suitable for glass processing. René Preßler adds: “We are talking about a particularly resilient backing, which does not suffer any permanent deformation under the enormous weight of the glass.”
Stephan Kammerer on the project at that time: “We used this special timing belt from Breco for the first time in 2020. The collaboration during development, the service life and the consistently good quality of the timing belt convinced us. This is why we approached Mr. Preßler from Hilger u. Kern after unresolved quality problems with our previous main supplier of timing belts. With him and Breco as the manufacturer, we recognised the potential to solve the technical challenges that still lay ahead. Even at that time, we understood how important the willingness and ability of a new main supplier of timing belts to carry out real development work would be for us.”
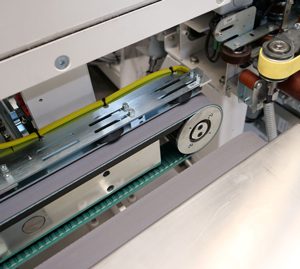
Breco timing belts are given different finishes on the tooth side, such as grooves, nips or a polyamide fabric, which reduces friction on the support rail and thus heat input, wear and drive power. Photo: Krismeyer
It is also important to know that over 100 different types of special timing belts are used in all Glaston machines and that up to 500 metres of these are installed in a single system. Their perfect functioning is system-relevant for the production of insulating glass and the requirements and environments in insulating glass production are extremely specialised:
- with water in the glass pane washer,
- for edge seaming (deburring) and edge stripping of glass with water and very abrasive glass dust,
- when drying the glass panes,
- there are also positioning applications in the tenth of a millimetre range, e.g. in the assembly and gas filling press.
The backs of the belts require a backing, which is precisely matched to the machine process. The extrusion of the backing onto the cold belt creates tension in the material at right angles to the tensile direction, which is noticeable in wider belts over 90 mm by a deformation of the belt – comparable to a bimetal. The belt bends like a bowl, which is what this flatness error is colloquially known as: Dishing.
Stephan Kammerer explains: “Our glass panes stand on the backing and due to the dishing of the timing belt on the support rail, the glass panes – especially light panes – cannot maintain their exact height position. Our systems can process a minimum format of 190 x 350 mm with a glass thickness of 3 mm – which weighs practically nothing. But they are also capable of processing glass weighing several tonnes at 2.7 x 6 m with a thickness of 45 mm.” The few tenths of a millimetre deviation due to the flatness error is irrelevant for most applications. However, this causes a positional deviation and is not desirable in insulating glass production.
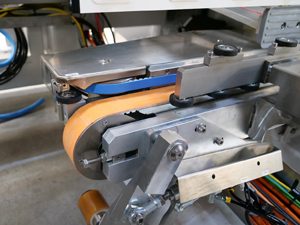
In the wet area: Even in constant exposure to water, the backings must ensure a certain adhesion value for slip-free transport. The blue backing must also be imprint-free on the glass. Photo: Krismeyer
Flatness in the tenth of a millimetre range
Stephan Kammerer on the procedure: “We then discussed the situation directly with Breco Managing Director Dr. Thomas Steinert in two video conferences. This resulted in new ideas for solving the problem and samples in various types, which we tested and which ultimately delivered the desired result.” The effort involved should not be underestimated, notes René Preßler: “Breco not only adjusted some production parameters to find a solution, but also used a new production process. I would like to state that there is no other manufacturer of timing belts with backing today, with such extensive know-how and excellent manufacturing expertise, as Breco. The results in terms of load bearing characteristics, consistent quality, in particular closely tolerated layer thicknesses and evenness are very impressive.”
Another advantage of the new timing belts with an extruded-on backing is that both the timing belt and the backing can be homogeneously joined together in a welding process. This eliminates the joint at the ends of the backing, which cannot be avoided with bonded backings. Glaston Purchasing Manager Martin Anthoni also spoke about this topic: “In the end, it wasn't just the technical requirements that were solved. The new process also made a significant contribution to reducing costs.”
Not all timing belts transport glasses upright over the longitudinal edge. Some timing belts also transport with the backing against the edge of the glass (in wet areas) or with flat support of the panes by means of negative pressure in the visible area. Unfortunately, imprints on washed glass cannot always be recognised 100% reliably, even under specially designed lighting and light colours for optical camera systems. Stephan Kammerer: “A clear full moon night with the insulating glass installed on the façade is ideal for detecting imprints. Only then it is far too late. There should be no imprints in the first place.”
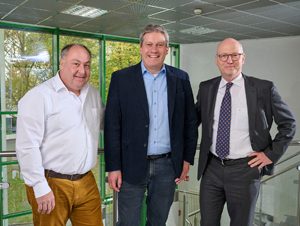
A successful team: (from left) René Preßler from Hilger u. Kern, Stephan Kammerer from Glaston and Dr.Thomas Steinert from Breco Antriebstechnik. Photo: Minkus Images
Direct line to the supplier's development
“Usually, we as a machine manufacturer, don't even get access to the leading developers at our suppliers. How this usually works: The contact persons at the supplier take up the complaint and forward the case to the quality control department. You receive a report and a new batch – and unfortunately the same problem again. Out of necessity, one begins to measure the timing belts individually so that machines can be delivered at all. That is not what we claim!” emphasises Stephan Kammerer and continues: “It was a special experience for us when there are people on the other side who know the production of the supplied part, in this case the timing belts, extremely well and in depth. This was the only way we could explain our needs in detail and Breco could ask questions until all aspects of the development task were properly understood. We also learnt immediately which measures have which effects on the product. And we were also able to ask questions until we understood what was planned on the other side. This took nothing away from the importance of the consulting engineer, Mr. Preßler from Hilger u. Kern. On the contrary, he was very closely involved in our changeover process to the new timing belts. In our particular case, direct communication with the manufacturer and development team was the only way to achieve our goal, and Breco was prepared to do this.”
The editorial team of Mulco took away one lesson from our visit: Listening carefully to the customer, fully understanding the task at hand, openness to new ways of communicating and producing on both sides and, of course, plenty of experience and very solid technical knowledge – when all of this comes together, sooner or later, success will follow. After more than two years of changing over, many different Breco special timing belts are now working reliably in the Glaston systems. Dishing is largely a thing of the past, as are complaints with respect to full moon nights. In Neuhausen in the northern Black Forest, all is right with the world again. And the rooster, yes, it's still crowing.
Garbsen, 22/05/2024
Mulco-Europe EWIV