Safe transport of electronic components
Safe transport of electronic components
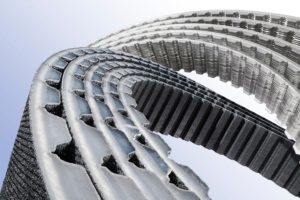
Antistatic BRECO timing belts made of conductive transparent TPU. The timing belts in the foreground are equipped with an additional conductive backing on the belt tooth side and back of the belt. Photo: Mulco
Where electro-static charging should or has to be avoided e.g. when transporting electronic components or in drives and conveyor systems in highly flammable environments, anti-static CONTI® SYNCHROFLEX, BRECO® and BRECOFLEX® timing belts are a safe option.
Electrostatic charging is the physical process by which an excess or shortage of electrons that cannot be compensated forms on non-electrically conductive surfaces. This potential difference usually does not pose a problem. However, if this charge is compensated by flashover and therefore strong pulsed discharge currents, damage may occur on sensitive components. In explosive environments these discharges may even pose a risk of ignition.
To protect electronic components in industrial environments from flashover, it is therefore required to continuously remove charge carriers (electrons) from the affected surfaces. Electrostatic charging of belt drives is primarily the result of sliding friction on guide and support rails, friction in the tooth mesh and electric fields. As the thermoplastic polyurethane (TPU) makes timing belts excellent insulators, dissipation of charge differentials can pose problems.
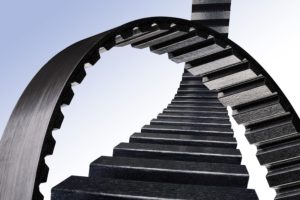
Antistatic CONTI SYNCHROFLEX timing belts made of conductive black PU compound. Photo: Mulco
To give timing belts antistatic properties, i.e. allow them to discharge electricity, a conductive material is mixed with the TPU. This creates a slightly conductive compound such as BRECO-TPU-AS1 with a resistance of < 10⁸ Ω. Significantly lower resistance values are achieved by the TPU compounds BRECO-TPU-AS2 and TPU-AS7. The latter is a recent development and offers particularly consistent resistance distribution in the longitudinal and transverse timing belt direction as well as very low resistance values < 10⁴ Ω.
Another option for making timing belts conductive is coating the tooth and/or belt back with a conductive backing. The antistatic PA backing created by BRECO offers a resistance value of 10⁵ Ω and is primarily used in belt drives serving as accumulating conveyors for electronic components. It also reduces the coefficient of friction to approximately 0.3.
CONTI SYNCHROFLEX polyurethane timing belts are also available with antistatic properties. A special conductive polyurethane compound is available up to a belt length of 700 mm. Alternatively, an electrically conductive backing can be applied post-manufacture.
Garbsen, 20.01.2023
Mulco-Europe EWIV